大Y洲成人小说网站——剧情小说
入口: 免费在线 ,好基友也在关注4438c最小脉冲宽度,提供高清在线免费也读,让您尽情感受激烈的比赛现场,全程无插件免费观看直播,为您呈现最热门精彩的在线小说!
1、激光焊接机的脉宽应该如何选择
激光焊接机脉宽是脉冲激光焊接的重要参数之-。它既是区别于打孔和焊接的重要参数,也是决定焊接质量的稳固可靠,供电电源体积庞大程度和成本高低的关键参数。当焊接工件确定后,脉宽的选取主要考虑以下3个因素:第一:为了达到一定的焊接强度要求,确定最小的熔深所需要的脉宽;第二:确定激光焊接机脉宽所对应的热通量密度的调整范围;第三:焊点的热损伤区。即在所允许的热影响区的限制下,可能选取的最大脉宽。对于一台脉冲能否稳固地运用于生产保证激光焊接机焊接质量是很重要的。激光焊接机脉宽的选择可按以下3个详尽的原则来确定:
(1)对于熔深需要在0.11mm以下的激光焊接,若对热影响区,或者说热损伤区有严厉的要求,则脉宽主要由热影响区来确定,即在热损伤区允许的情况下,脉宽选在1.5ms左右为好。
(2)对于熔深需要在0.1-0.2mm、对焊点仅有强度要求、对热影响区无严厉要求的一类单次脉冲微型焊接,大部分金属的激光脉宽选择在3ms左右。对此类,脉宽的选取主要决定于焊点形成牢固可靠的熔融焊接时,热通量密度变化的可允许范围。
(3)熔深要求大于0.33mm的一类焊接,脉宽选取主要决定于熔深。
2、什么是脉冲宽度,脉冲间隔
一、脉冲宽度
释义:不同的领域,脉冲宽度有不同的含义。通常的脉冲宽度是指电子领域中,脉冲所能达到最大值所持续的周期。"脉冲宽度" 在学术文献中的解释。
1、脉冲光源的闪光持续时间是指1/3峰值光强所对应的时间间隔称为脉冲宽度。它主要由光源的结构和点灯电路决定。在小城镇使用时对显色性要求不高一般可采用高压钠灯或金卤灯。
2、脉冲宽度是指电磁阀开启的时间长度。渣油分散体系的这一最佳活化状态,不但与油浆掺炼率有密切关系,还与操作条件以及渣油的性质有关。
3、脉冲所能达到的最大值称为“脉冲宽度”。形状、幅度和宽度是脉冲的主要参数。周期性重复的脉冲每秒出现的个数称为“脉冲频率”,其倒数称为“脉冲周期”。
4、这里m是任意正整数每个子区间的长度(h=T/m)称为脉冲宽度。作为一个例子对于m=4时的情况在图1中表明。若问题是在区间τ∈ab)那么通过作变换t=(τ-a)T/(b-a)就可把问题转换到区间t∈0T)上的等效问题。
二、脉冲间隔就是上一脉冲与下一脉冲的时间间隔。脉冲信号是一种离散信号,形状多种多样,与普通模拟信号(如正弦波)相比,波形之间在时间轴不连续(波形与波形之间有明显的间隔)但具有一定的周期性是它的特点。
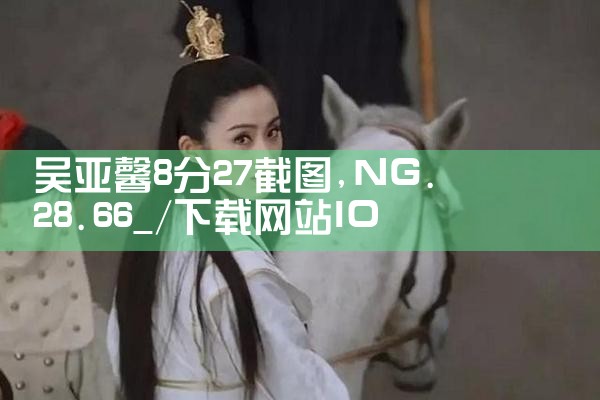
3、电火花下切割加工技术论文
电火花下切割加工在实际生产加工中应用非常广泛,特别是在冲压模具加工中是最为理想的加工设备,在加工过程中加工参数的调整时影响工件质量的重要因素。我为大家整理的电火花加工技术论文,希望你们喜欢。
电火花加工技术论文篇一
浅谈电火花线切割加工工艺
摘要:文章针对电火花线切割加工的工艺及对工件材料的预处理、穿丝孔的加工进行了分析,明确了线切割加工前工件的预处理方法,对实际工件的线切割加工路线设计起到了指导作用。
关键词:退磁处理;预处理;穿丝孔;线切割;电火花加工
中图分类号:TG661文献标识码:A文章编号:1009-2374(2014)22-0131-02电火花加工是利用能量密度很高的电火花,使工件材料熔化、气化和蒸发而去除的一种特种加工方法。电火花线切割加工是电火花加工中的一种,利用金属丝做线状电极,对工件进行切割。下面对线切割加工中的工艺问题进行分析。
1工件材料的预处理
锻造和淬火的工件材料在加工前需要进行预处理。锻打的淬火后的材料会有不同的残余应力。在大面积去除切割和切断加工中,由于残余应力的相对平衡受到破坏,在加工过程中应力会释放,从而导致工件变形,达不到尺寸精度要求。淬火不当的材料还会在加工中出现裂纹。因此这样的材料在线切割加工前,一般应进行低温回火处理。
经过热处理的工件,需将工件上电极丝起割处的热处理残余物、氧化皮和锈斑清除。因为这些残余物不导电,电极丝极容易产生断丝、烧丝或者使工件表面出现深痕,严重时使电极丝离开加工轨迹,造成工件报废。若工件需要机械加工的方法(如车削、铣削等)加工外形及定位面,应注意棱边倒角,孔口倒角。以磨削加工定位面,需对工件材料进行消磁处理。
2穿丝孔的加工
穿丝孔是电极丝相对工件运动的起点,同时也是程序执行的起点,一般选在工件上的基准点处。
2.1穿丝孔(又称工艺孔)的作用
(1)用于加工凹模。凹模类封闭工件在切割前必须具有穿丝孔,以保证工件的完整性。(2)减小凸模加工中的变形量,防止因材料变形而发生夹丝、断丝现象。(3)作为定位基准,保证被加工部位与其他部位的位置精度。对于前两个作用来说,穿丝孔的加工精度要求不需过高。但是对于第三个作用来说,就必须考虑其加工精度。
2.2穿丝孔的位置
穿丝孔的轮廓和加工零件轮廓的最小距离与工件的厚度有关。工件越厚,则最小距离越大,一般不小于3mm。对于凸模类、凹模类工件,穿丝孔轮廓到工件的加工轮廓的最短距离≥3mm。对于凸模类工件,为减小变形,工件的加工轮廓到坯料侧面的距离≥5mm,工件的加工轮廓到坯料尖角处的距离≥8mm。线切割加工用的坯料在热处理时,表面冷却快,内部冷却慢,形成热处理后坯料的金相组织不一致,产生内应力,并且越靠近边角处,应力变化越大。所以,线切割的图形轮廓应尽量避开坯料边角处,避免变形影响工件精度,一般让出8~10mm。对于凸模还应留出足够的夹持余量。
选取穿丝孔时,应遵循以下原则:
加工凹模(型孔类工件):(1)小的型孔切割,穿丝孔设在型孔中心。在切割中、小孔形凹模类工件时,穿丝孔应选在凹型的中心位置最为方便。因为这样既能使穿丝孔的加工位置准确,又能便于控制坐标轨迹的计算。(2)大的型孔切割(或凸型工件),穿丝孔设在靠近加工轨迹的边角处或者已知坐标尺寸的交点上,以便简化运算过程。在切割凸型工件或大孔形凹型工件,穿丝孔不宜选择凹型的中心,因为这样将使无用行程的切割路径较长。所以此类切割一般选择起割点附近为好。(3)多型孔切割,每个型孔都有各自独立的穿丝孔。
加工凸模(轮廓类工件):(1)凸型工件(或大的型孔)切割,穿丝孔在靠近加工轨迹的边角处,即起割点附近。穿丝孔的位置可选在加工图形的拐角附近,以便简化编程运算,缩短切入时的切割行程。(2)封闭式切割,而非开放式切割,否则破坏残余内应力的平衡状态,引起变形。如图1(a)所示,许多模具制造者在切割凸模类外轮廓工件时,常常直接从材料的侧面切入,在切入处产生缺口,残余应力从缺口处向外释放,容易使凸模变形。为了避免变形,在淬火前先在模坯上打出穿丝孔,孔径为3~10mm,工件淬火后从模坯内部对凸模进行封闭式切割。(3)由外向内切割。如图1(b)所示,对于零件,特别是凸模类工件,切割方向可采用由外向内切割。切割方向应该有利于保
《小老板|SERVICE》尊享免费大平台
入口: 免费在线
提供高清在线免费也读,让您尽情感受激烈的比赛现场,全程无插件免费观看直播,为您呈现最热门精彩的在线小说!